Wieder ein Projekt für einen sehr lieben Menschen: ein Anlehnregal!
So ein Anlehnregal ist ein höchst dekoratives Möbelstück für besondere Bücher, Fotos oder auch Bilder. Es muss nicht an die Wand montiert werden und kann je nach Geschmack zwischendurch umgestellt werden. Es nimmt auch nicht viel Platz weg, weil es nur etwa 70 mm tief ist.
Dabei ist es gar nicht so schwer zu bauen. Ich nutze für den Bau meinen Duodübler, um nicht sichtbare Dübelverbindungen zu machen. Du kannst natürlich auch Schraubverbindungen einsetzen und die Löcher später überspachteln.
Ich beschreibe hier übrigens den Bau des zweiten Anlehnregals, weil ich beim ersten Mal vergessen habe Bilder zu machen. Das zweite ist für mein frisch renoviertes Esszimmer.
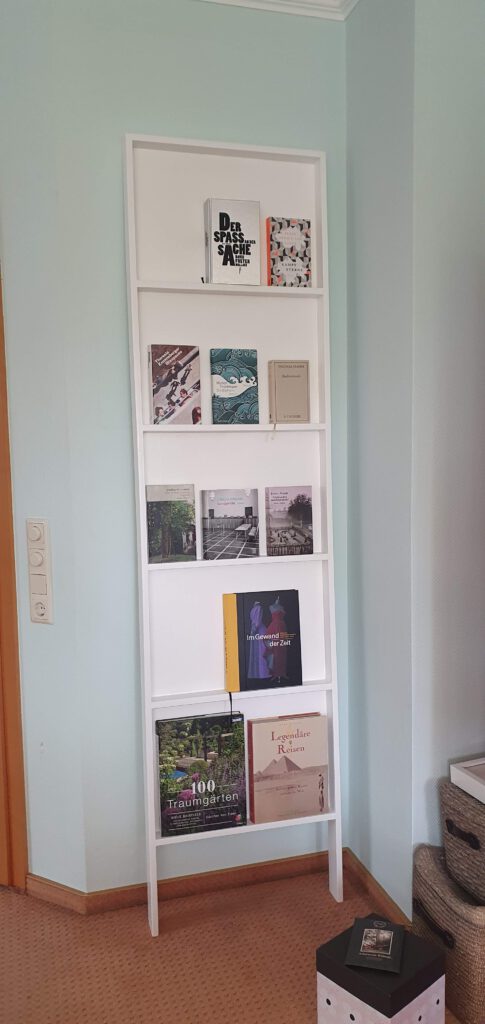