… oder “pimp up my welder”!
Wie du als Stammleser natürlich weißt, besitze ich seit geraumer Zeit ein Schutzgas-Schweißgerät, welches ich bei einigen Projekten bereits fleißig im Einsatz hatte.
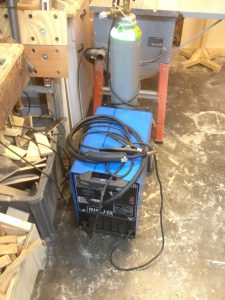
Während dieser Einsätze zeigen sich natürlich die Schwachstellen, bzw. das Verbesserungspotential und irgendwie hatte ich das überaus dringende Bedürfnis, dieses Potential zu nutzen. Wer mich und meinen Blog kennt, ist sich schon jetzt gewiss, dass dabei irgendetwas schief läuft etwas zu lernen gibt und ich es aber überraschenderweise wieder hinkriege… ja, das war hier auch so… du kennst mich einfach zu gut…:-)
Folgende Dinge haben mich also beim Arbeiten mit dem Güde MIG 170 gestört:
- zu kurzes Massekabel
- zu kleine Masseklemme
- zu kurzes Schlauchpaket
- zu hoher Druckpunkt beim Schalter am Brenner
Folgende Lösungen habe ich mir dafür überlegt:
- langes Massekabel
- größere Masseklemme
- längeres Schlauchpaket
- anderen Brenner
Äh…, ja das klingt jetzt nicht sehr überraschend oder innovativ, aber um diese Lösungsansätze hinzukriegen, mussten umfangreiche Umbaumaßnahmen durchgeführt werden.
Die Masse-Geschichte wäre kein Problem. Anderes Kabel mit einer anderen Klemme anbasteln, fertig. Aber das wäre ja zu einfach. Für das Schlauchpaket geht das zum Beispiel nicht.
Ich habe aber herausgefunden, dass es sogenannte Euro-Anschlüsse für Schweißgeräte gibt. Das sind genormte Anschlüsse, die es dir erlauben, das Schlauchpaket unkompliziert auszutauschen. Für das Massekabel gibt es Bajonettverschlüsse in unterschiedlichen Größen, so dass du auch das Massekabel jederzeit tauschen kannst, ohne das ganze Gerät auseinander nehmen zu müssen. Diese Anschlüsse gibt es bei Ebay und rate mal, wer sich umgehend so etwas gekauft hat… 🙂
ABER (Jetzt kommts):
Es gibt Gründe, warum der Schalter an meinem Brenner so schwer zu schalten ging. Unter anderem wird mit ihm das Ventil für das Schutzgas betätigt, welches im Brenner sitzt. Der Gasdruck steht also bis zum Brenner ständig an. Das war auch der Grund, warum ich meine Gasflaschen bei Nichtgebrauch immer zugedreht habe… sie waren sonst am nächsten Tag leer… das Ventil war wohl nicht ganz dicht.
Um den Euro-Anschluss einbauen zu können, muss das Gas über ein Magnetventil geschaltet werden, weil der Brenner nur einen Schalter für den Schweißvorgang beinhaltet. Das Gas würde also ohne Magnetventil dauerhaft ausströmen. Also habe ich mir ein passendes Magnetventil gleich mitbestellt.
Folgende Materialien habe ich bestellt:
- Magnetventil für Gasanschluss ca. 14 €
- Schlauchpaket mit Brenner und Euro-Anschluss – 4 Meter ca. 30 €
- Buchse Euro-Anschluss mit Kragen, Schlauch und Kabel ca. 17 €
- Massekabel mit Klemme – 5 Meter ca. 35 €
- Bajonett-Buchse für Massekabel ca. 5 €
Für diese ganzen tollen Sachen habe ich also etwa 100 € bezahlt. Find ich OK.
Ach ja… kurzer Hinweis in eigener Sache:
Der Umbau eines Schweißgerätes bedingt, dass man in der Elektrik, bzw in der Elektronik Veränderungen durchführt.
DAS IST NICHT GANZ UNGEFÄHRLICH!!!
Ich bin ein ausgebildeter Energieelektroniker, habe also zumindest ansatzweise Ahnung von der Materie. Bitte fummel nicht einfach an deinem Schweißgerät herum, wenn du nicht genau weißt, was du tust. Dieser Artikel soll lediglich der Unterhaltung dienen und ist
KEINE VERBINDLICHE ANLEITUNG!!!
Deshalb gehe ich auch nicht sehr stark auf die technischen Details ein. Du wirst gleich sehen, warum ich das so betone…
Umbau des Massekabels
Fangen wir mit dem einfachsten an: dem Ausbau des kurzen Massekabels und dem Einbau der Massebuchse.
Vom Trafo kommen der Plus- und der Minuspol an zwei Schraubklemmen an.
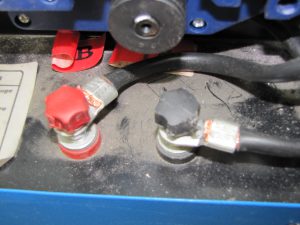
Das neue Massekabel hat einen Querschnitt von 25 mm² und deshalb habe ich von der Klemme auch mit einem Stück 25 mm² Kabel die Verbindung zur Massebuchse hergestellt. Dazu habe ich passende Kabelschuhe aufgequetscht. Das kurze Stück Massekabel, sowie die 25 mm² Kabelschuhe habe in der Yacht-Abteilung im Baumarkt gekauft (Batteriezubehör). Die Massebuchse wird mit einer Kontermutter in die Blechverkleidung des Schweißgerätes verschraubt. Die vorhandene Öffnung hatte sogar eine Aussparung für die “Nase” der Buchse, so dass ich an der Öffnung keinerlei Veränderungen vorzunehmen brauchte. Die Nase verhindert später das Drehen der Buchse beim Einschrauben des Steckers. Der Kabelschuh des Massekabels wird einfach auf das vorhandene Gewinde aufgeschraubt… fertig!

Ich war von dem Material und meinen unglaublichen Fähigkeiten so dermaßen beeindruckt, dass ich gleich den nächsten Schritt anging:
Einbau des Magnetventils
Das Magnetventil weist drei Anschlüsse in Form von Flachsteckern auf. Da es sich ja bei diesem Bauteil um eine Spule handelt, die angesteuert wird und dann das Ventil öffnet, ist es nicht schwer herauszufinden, welche die richtigen Anschlüsse sind. Ich habe mit meinem Messgerät gemessen, welche beiden Anschlüsse eine elektrische Verbindung hatten (Spule) und quetschte auf zwei flexible Leitungen jeweils einen Kabelschuh. Die Masse schloss ich an den Masseanschluss an, der vom Netzkabel kam. Doch jetzt wurde es kniffelig. Das Magnetventil soll nur dann aufmachen, wenn ich den Schalter drücke und schweißen will. Ich musste also den Anschluss des Trafos suchen und den Weg zu dem jeweiligen Schaltrelais finden. Da nahm ich die Spannungsversorgung für das Magnetventil ab und fertig… dachte ich… aber gehen wir weiter.
Das Magnetventil wurde mit zwei Schlauchtüllen geliefert, die eingedreht werden und wo der Schlauch nur darüber gezogen wird. Eine Schlauchtülle drehte ich durch das Blechgehäuse mit U-Scheibe und Gummidichtung in das Ventil, so dass es stramm innen am Gehäuse sitzt und dicht ist… dachte ich… aber gehen wir weiter.
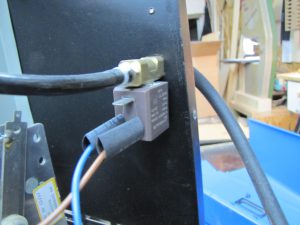
Einbau des Euro-Anschlusses
Davor hatte ich am meisten Respekt. Der Anschluss muss nicht nur an den “Pluspol” des Trafos angeschlossen werden, sondern er muss auch so sitzen, dass der Drahtvorschub den Schweißdraht gerade in die Seele des Schlauchpaketes führen kann. Auch hier war ich von der Qualität der bestellten Ware wirklich sehr angetan. Mit einem Stück 15 mm Siebdruckplatte konnte ich den Anschluss mit dem Montagekragen so am Gehäuse befestigen, dass alles richtig saß.
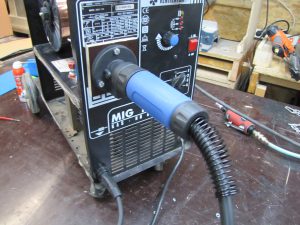
Mit einem Stück 25 mm² Massekabel und zwei Kabelschuhen, wurde der Euro-Anschluss mit dem Trafo verbunden, den Schlauch führte ich zum Magnetventil und befestigte ihn an der Schlauchtülle mit einem Kabelbinder – nur zur Sicherheit…
Jetzt fehlten noch die beiden Leitungen, die vom Schalter des Brenners, bzw. des Euro-Anschlusses kamen. Sie mussten so an der Steuerplatine angeschlossen werden, dass das jeweilige Relais schalten kann. Auch das war nicht sehr schwer zu ermitteln. Ich folgte im Vorwege, also bevor ich das alte Schlauchpaket ausbaute, den Steuerkabeln und ermittelte die richtigen Anschlüsse. Auch hier kamen Kabelschuhe zum Einsatz.
Nachdem alles angeschlossen war, kam der Testlauf. Nun bin ich aufgrund meiner Ausbildung ziemlich vorsichtig, wenn ich umgebaute Geräte das erste Mal teste. Zum Glück!
Das Drama beginnt…
1. Akt: Strom lügt… eigentlich…
Ich stellte das Schweißgerät so hin, dass ich es von etwa zwei Metern Entfernung einschalten und den Schalter am Brenner betätigen konnte. Ich schaltete das Gerät ein und der Lüfter lief erwartungsgemäß an. Super. Ich betätigte den Schalter am Brenner und …. alles war dunkel…
Ein Hoch auf Gottfried Biegelmeier, dem Erfinder des FI-Schutzschalters!
Ja die Sicherung fiel und der Haupt-FI-Schutzschalter gleich mit. Hmmmm…
Ich trennte alles vom Netz, drückte Sicherung und FI wieder rein und machte mich auf die Fehlersuche. Augenscheinlich gab es keinerlei Schäden am Schweißgerät, keine Versengungen oder ähnliches.
ich verfolgte die neu angeschlossenen Leitungen und war mir sicher alles richtig angeschlossen zu haben. Ich zog die Ansteuerung für das Magnetventil ab und versuchte es nochmal. Gerät einschalten… Lüfter läuft… Schalter am Brenner betätigen… Drahtvorschub läuft… Hmmmm komisch. Der Fehler lag also an der Ansteuerung für das Magnetventil. Ich überprüfte alles nochmal und kam zu dem Schluss, dass sich alle Sicherheitseinrichtungen und auch der Strom an sich einfach nur geirrt hatten. Kann ja mal vorkommen… (Spätestens hier erkennst du die massive Baudiele, die sich vor meinem Kopf befand…) Im Nachhinein könnte ich mir immer noch in den A….rm beißen.
In der Gewissheit, dass sich Alles und Jeder außer mir irrte, schloss ich alles genauso an, wie vor dem Knall und probierte es nochmal aus. Das Ergebnis ist jedem normaldenkendem Heimwerker klar: es knallte wieder und diesmal waren auch zwei Leiterbahnen auf der Platine verraucht. Nachdem ich mit meinem Messgerät auf Fehlersuche ging, stellte ich schnell fest, dass das Steuerrelais seiner Empörung über mein stümperhaftes Verhalten mit kontinuierlichem Durchgang Ausdruck verlieh… Und erst jetzt fielt mir auf, dass ich …Simsalabim… die Anschlüsse am Magnetventil vertauscht hatte… Ich habe einen Kurzschluss hergestellt… zweimal hintereinander…! Bravo Kellerwerker!
Zum Jammern fehlte mir die Lust, also suchte ich im Internet nach einem Ersatzrelais und bestellte ein Neues in… Italien… über Ebay… wo sonst? In ganz Deutschland gab es keinen Ersatz. Also nochmal 12 € investiert und vier Tage warten, bis es geliefert wird. In der Zwischenzeit reparierte ich die Platine.
Statt einem kamen vier Relais. Ok nicht schlimm. Wenn du mal eines brauchst, schick mir eine Mail. Kostet nur 12€… Freundschaftspreis…:-).
Nachdem ich das Relais ausgetauscht und die Verdrahtung korrekt hergestellt hatte kam der Probelauf und die Begeisterung war wieder da! Es funktionierte tadellos… fast… na ja eigentlich stotterte der Lichtbogen beim Schweißen ständig. Okay, eine vernünftige Naht war nicht herzustellen… Hmmmm…
2. Akt: Kunststoff gibt auf Dauer nach
Die Ursache: der Drahtvorschub. Es lag weniger an der Kraft des Motors, als vielmehr an der Billig-Verarbeitung des Gehäuses. Alles Kunststoff. Das Kugellager, das den Gegendruck zur Antriebswalze aufbaut steckt in einem Kunststofflager, das im Laufe der Zeit ausgniedelte. (Ein weiterer Begriff für Manuels Heimwerker-Lexikon). Das eigentliche Problem ist aber die Lagerung der Antriebswelle.
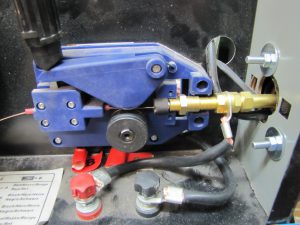
Sie eiert, weil sie nur durch ein Kunststofflager gehalten wird. Durch dieses Eiern hat der Drahtvorschub keine Kraft den Schweißdraht durch das ohnehin längere Schlauchpaket zu transportieren. Wenn dann noch das Schlauchpaket nicht ganz gerade liegt stottert der Drahtvorschub und der Lichtbogen reißt ständig ab.
Die Lösung: einen neuen Drahtvorschub kaufen. Ich habe gleich bei Ebay geschaut und eins gefunden. Nochmal 50 €. Aber Aufgeben war keine Option!
Der neue Drahtvorschub kam und ich überlegte also, wie ich ihn am besten einbauen könnte.
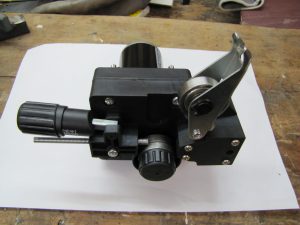
Es traf sich ganz gut, dass der neue Drahtvorschub, etwa gleich groß ist, wie der alte. Trotzdem musste ich das Loch des Bleches, an dem der Drahtvorschub befestigt werden sollte, vergrößern. Oder?
Nö. Ich fand die ganze Blechgeschichte an dem Schweißgerät sowieso beschämend. Gerade dieses Blech, das etwas Stabilität für den Drahtvorschub geben sollte, wabbelte (Manuel…) wie Zeitungspapier. Die Lösung lag nahe, ein zusätzliches Blech einzusetzen.
Ich fertigte also ein 3 mm starkes Blech an, sägte die Ausschnitte für die Kabel und Schläuche und bohrte 5 mm Löcher für die Poppnieten, mit denen ich das Blech befestigen wollte.
Ich war nun soweit frei, was die Platzierung des Drahtvorschubs anging und musste somit den Euro-Anschluss nicht auch noch versetzen. Nur eine Stelle der großen Öffnung musste für den Euro-Anschluss mit dem Druckluftgeradeschleifer nachgearbeitet werden, weil das Blech nun mal 3 mm auftrug. Na ja und die drei Bohrlöcher mussten zu Langlöchern umgearbeitet werden, weil ich ja nicht ganz genau wusste, wie der Anschluss sitzen musste… Also wieder eine riesen Fummelarbeit alles ganz einfach und schnell gemacht…
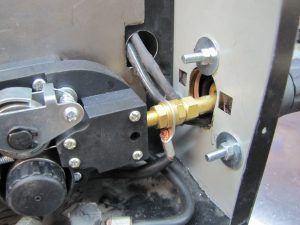
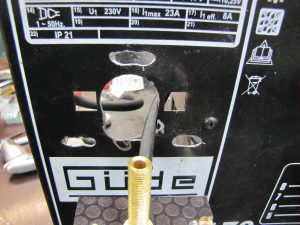
Ich zeichnete den späteren Sitz des Drahtvorschubs an und flexte die Öffnung ein. Jetzt konnte ich die Löcher für die Durchgangsverschraubung, sowie für den Halter der Drahtrolle anzeichnen und bohren. Das Blech befestigte ich mit Poppnieten und setzte dann den Drahtvorschub ein.
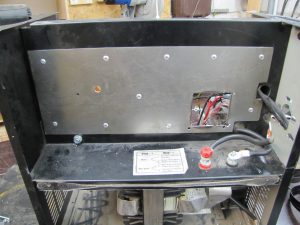
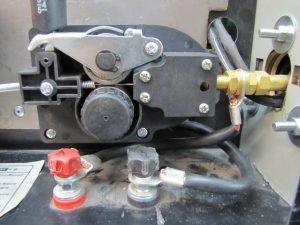
Alles wurde ordentlich befestigt. Ich setzte den Draht in die Seel und schob ihn die ersten paar Zentimeter von Hand ein. Nachdem ich die Kabel auf die Anschlüsse am Motor gesteckt hatte, startete ich den Testlauf.
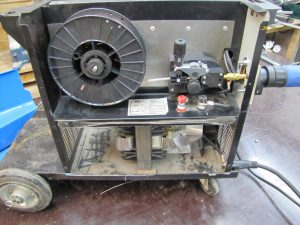
Trommelwirbel und… zack die Bohne… alles klappte wie am Schnürchen! Anfangs stotterte es ein wenig, aber der Draht musste ja auch erstmal durch das ganze Schlauchpaket geführt werden. Als er dann austrat und ich etwa 50 cm durchlaufen ließ, lief alles gleichmäßig.
Fertig!
Ach nee, doch nicht… Als ich so verträumt und selbstverliebt auf das innere meines schönen Schweißgerätes schaute, bemerkte ich ein sanftes Zischen. Nachdem ich mich drauf konzentrierte, fand ich die Leckage. Der Gasanschluss des Magnetventils war nicht dicht. Ich hatte ihn nur mit einer Dichtung versehen, die ich von außen zwischen Blechwand und Schlauchtülle anbrachte. Das reichte nicht, aber eine zweite Dichtung, die hinter der Blechwand sitzen sollte passte wegen des kurzen Gewindeteils nicht auf die Schlauchtülle. Kurzerhand schaltete ich meine Heißklebepistole an und verlegte das Magnetventil. Ich klebte es mit einer ordentlichen Portion Heißkleber an die Innenwand. Die beiden Schlauchtüllen schraubte ich ordentlich fest und Jetzt zischte gar nichts mehr. Danach konnte ich die Kabel ordnen und mit Kabelbindern fixieren.
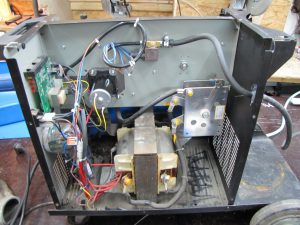
Ein letzter Testlauf und danach schraubte ich alles wieder zu.
Fertig!
Jo, jetzt wirklich…
Rückblickend würde ich sagen, dass ich für die etwa 150 € Investition jetzt ein Schweißgerät besitze, wie es mir schon immer gewünscht habe… Ich habe damals 180 € für das gebrauchte Schweißgerät bezahlt, macht also zusammen 330 €. Das ist noch im Rahmen. Hätte ich aber vorher gewusst, welchen Aufwand ich betreiben müsste, hätte ich doch gemacht. 🙂 Es war zwar zeitweise etwas frustrierend, aber ich habe mal wieder einiges gelernt und es hat Spaß gemacht!
Falls du mal dein Schweißgerät auch so umbauen möchtest, wie ich, dann viel Glück… 🙂
Herzliche Grüße
Frank
-der Kellerwerker