Die Flachdübel sollen grundsätzlich erstmal zwei Latten stumpf verbinden. Die Stirnseite einer Latte trifft auf die Längsseite einer anderen.
Ich überlegte mir also als erstes, wie ich eine Nut in die Stirnseite einer 75x35mm Latte fräse und was für eine Führung ich für ein immer gleichbleibendes Ergebnis benötige.
Ich probierte erstmal mit einer 10mm Sperrholzplatte herum, in die ich eine Öffnung sägen wollte, die genau 75x35mm maß.
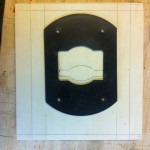
Ich nahm die abnehmbare Grundplatte als Messhilfe und mass sowohl die Breite als Führung, sowie die Länge inklusive 35mm Nutlänge ab. Im Falle meiner Oberfräse hat die Grundplatte 110x155mm). Vom Zentrum aus maß ich nun die 75x35mm ab und sägte die Öffnung aus.
Um die Latte gerade einzuspannen, befestigte ich mit Leim und Schrauben zwei Abschnitte einer identischen Latte jeweils an den kürzeren Seiten. Wenn ich jetzt die Schablone mit der Latte in meine Vorderzange einspanne, sitzt sie absolut gerade und ich kann darauf mit der Oberfräse arbeiten. Später habe ich die Kanten der Unterseite der Öffnung mit einer Phase versehen, damit sich das Werkstück leichter einführen läßt. Außerdem habe ich die beiden Leisten und die Lauffläche der Fräse mit Antikwachs behandelt, damit alles besser flutscht…
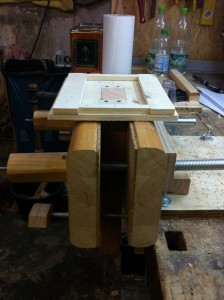
Als Führung leimte und tackerte ich Sperrholzabschnitte auf die Platte.
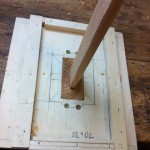
Das funktionierte super und ich fertigte gleich noch eine Schablone für die Lattenstärke 75x45mm an. Ich kann damit eine Nut mit den Maßen 35x10mm fräsen.
Die Flachdübel fertigte ich aus Resten in den Abmessungen 30x10mm an. Die Kanten habe ich mit dem Hobel abgerundet.
Nun kam aber die größere Herausforderung: Wie fräse ich die Nut in das Längsholz? Vor allem, wie fertige ich eine Schablone an, die sich verstellen lässt, damit ich unterschiedlich breite Werkstücke bearbeiten kann?
Leider wurde ich im Internet nicht fündig, so dass ich in meinem Skizzenbuch verschiedene Entwürfe zeichnete und schließlich in der Werkstatt einfach anfing.
Für diese Schablone nahm ich 12mm Multiplex Birke.
Ursprünglich wollte ich die Schablone so anfertigen, dass ich die Wege der Oberfräse sowohl in Längs- als auch in Querrichtung verstellen konnte.
Diese Idee verwarf ich aber wieder. Ich wollte mich auf die gleichbleibenden 30mm breiten Flachdübel konzentrieren. Also musste nur die Querrichtung verstellbar sein, um Werkstücke in unterschiedlichen Stärken bearbeiten zu können.
Die Abmaße in Längsrichtung ist somit immer 180mm.
155mm ist die Grundplatte der Fräse lang zuzüglich 35mm Nut ist gleich 190mm –
aaaaber: der Weg der Fräse ist nur 25mm, weil vom Zentrum des Fräsers noch zusätzlich 5mm zu jeder Seite hinzukommen. Der Fräser hat ja einen Durchmesser von 10mm… Das habe ich natürlich zuerst auch falsch gemacht – allerdings bei den Schablonen für die Stirnseite, so dass ich das bei dieser Schablone gleich berücksichtigte. Ich alter Fuchs ich…
Ich sägte mir also zwei Stücke in 100x280mm zurecht. Diese dienen rechts und links von der Latte als Anschlag. Für die obere Begrenzung sägte ich zwei Brettchen mit den Maßen 50x300mm zurecht.
Diese Brettchen sollten mit dem linken Anschlag fest verbunden und jeweils mit einem Langloch an den rechten Anschlag geschraubt werden.
Dadurch, dass diese beiden Brettchen quasi oben auf den seitlichen Anschlägen liegen, liegt die Oberfräse bündig auf dem Werkstück auf.
Jetzt fehlen noch der seitlichen Anschlag für die Fräse. Diese sägte in in Form zweier Brettchen (180x100mm) aus. Auch diese Anschläge erhielten jeweils mittig ein Langloch, damit sie verstellbar sind.
Zu guter Letzt sollte für die Stabilität ein Winkel, der später am Werkstück nach unten verläuft sorgen. Diese beiden Winkel sind länger als die gesamte Konstruktion, damit ich das ganze am Werkstück mittels Schraubzwungen fixieren kann.
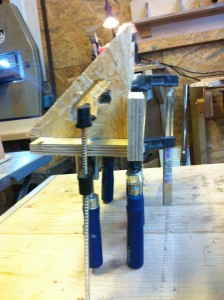
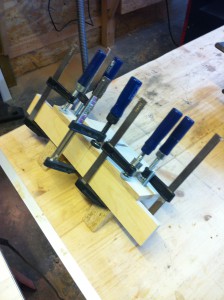
Später musste ich den Winkel kürzer sägen, weil ich sonst die zu bearbeitende Latte nicht lang genug in den Schraubstock einspannen konnte. Ursprünglich waren die Winkel 50mm lang (nach unten gemessen), später sägte ich sie auf 30mm.
So sieht sie zusammengebaut aus: die Frässchablone! Auch hier bearbeitete ich die Laufflächen der Oberfräse mit Antikwachs.
Die Mitte in Längsrichtung habe ich sehr sorgfältig gemessen und an beiden Seiten eine Kerbe mit der Säge eingesägt. Zur Funktionsweise:
Das Werkstück wird eingespannt, das zu verbindene Teil wird angesetzt und markiert.
Dabei wird nur die Längsseite angezeichnet. Die Mitte ergibt sich durch die Schablone. 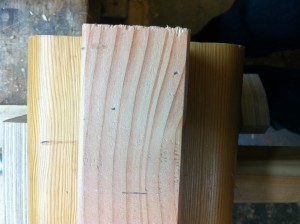
Anschließend wird die Mitte in Längsrichtung markiert und mit einem Winkel angezeichnet.
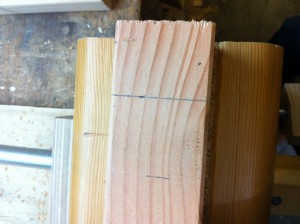
Jetzt wird die Schablone vorbereitet. Die seitlichen Anschläge werden gelöst und die Schablone wird stramm an das Werkstück gelegt. Die beiden seitlichen Anschläge liegen nun an und werden mit den Muttern fixiert.
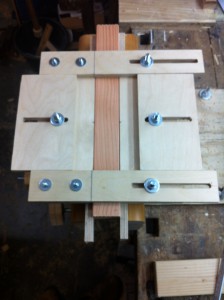
Die Grundplatte der Oberfräse ist 110mm breit. Von der Mitte des Werkstücks bis zum linken seitlichen Anschlag der Oberfräse sind es also 55mm, von denen 22,5mm abgezogen werden müssen. Das heißt, vom seitlichen Anschlag des Werkstücks bis zum linken Anschlag für die Oberfräse müssen 32,5mm eingestellt werden.
Der Oberfräsenanschlag wird befestigt und der rechte Anschlag wird einfach mit Hilfe der Oberfräse eingestellt. Die Oberfräse wird stramm an den linken Anschlag angehalten und der rechte Anschlag wird stramm an die Oberfräse angelegt und festgestellt.
Die mittlere Markierung der Schablone wird mit der Markierung auf dem Werkstück ausgerichtet und mit zwei Zwingen befestigt.
Jetzt muss nur noch die Tiefenbegrenzung an der Oberfräse so eingestellt werden, dass der Fräser 30mm tief fräst.
In mehreren Arbeitsgängen wird nun die Nut ausgefräst…
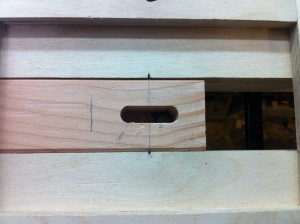
…der Flachdübel eingesetzt…
…das Gegenstück angesetzt…
… und eingepaßt.
Jetzt wird alles ordentlich verleimt und fertig ist die Verbindung!
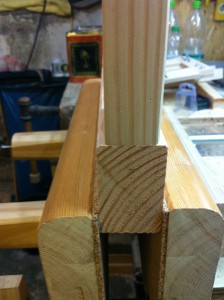
Hier seht Ihr das erste Geländerelement, welches ich mit den Frässchablonen gebaut habe.
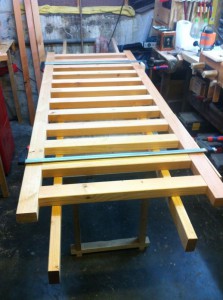