Der gesamte Tisch besteht aus einer Tischplatte, zwei höhenverstellbaren Beinen, die durch einen Ablagekasten verbunden sind, sowie einer Schublade.
Die Füße und Beine
Den gesamten Tisch habe ich aus Materialien hergestellt, die ich in meiner Werkstatt liegen hatte. Ausgenommen die Beine wurden aus 10 mm Sperrholzbrettern gebaut, welches ich mir aus dem Baumarkt gekauft habe.
Die Füße bestehen aus einer Leiste 30 x 30 mm, an die ich an der Unterseite des Fußes vorne und hinten jeweils einen 4 cm langen Klotz aus der gleichen Leiste angeklebt habe.
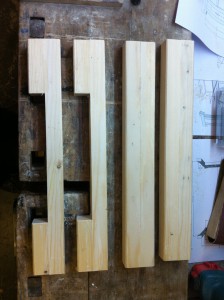
links die Füße, rechts die Tischanschläge
Die Enden wurden dann mit der Kreissäge und meinem Schiebeschlitten angeschrägt.
Die Verbindung zwischen Beinen und Tischplatte wurde mit einem Tischanschlag hergestellt, der auch aus den 30 x 30 mm Leisten besteht. Hier habe ich zwei Stück in gleicher Länge (440 mm) zusammengeleimt.
Es folgten die Beine, die eigentlich nur aus zwei Ständern mit Feder und einem darin laufendem Bein mit einer Nut auf beiden Seiten bestehen. Das “laufende Bein” (klingt wie der Name eines stolzen Indianers…) wird mit der Tischplatte verbunden, die somit höhenverstellbar ist.
Die Ständer wurden mittig mit einer 10 mm Nut versehen, in die ich die Feder einleimte. Die Feder besteht aus dem 10 mm Sperrholz und stand ca. 20 mm aus der Nut heraus.
Das “laufende Bein” (ich find den Namen so toll…) besteht aus drei verleimten Brettern des oben beschriebenen 10 mm Sperrholzes, wobei die mittlere Platte um 22 mm auf jeder Seite schmaler als die äußeren Bretter sind. Damit haben wir die Nut für das laufende Bein (ich hör schon auf…) geschaffen ohne groß fräsen zu müssen.
Die Ständer werden auf die Füße montiert. Ich habe dazu die Maße der Sperrholzkonstruktion (ich habe nicht laufendes Bein geschrieben) als Maß für den Abstand der Ständer genommen.
Die Ständer habe ich von unten durch die Füße verschraubt und verklebt. Damit das Sperrholz (!) leicht in den Ständern läuft bedarf es der Bearbeitung mit Schleifpapier. Ich erhielt später den Tip, dass man auch Wachs nehmen kann, habe es aber nicht ausprobiert.
Das Sperrholz wird auf der anderen Seite mit dem Tischanschlag verbunden, der nachher auf der Tischplatte befestigt wird. Auch hier habe ich durch die Leiste ins Sperrholz geschraubt und zusätzlich verleimt. Vorbohren nicht vergessen!
Die Tischbeine sind nun fast fertig! Es müssen noch drei Bohrungen, sowie jeweils drei Dübel gesetzt werden. Das habe ich aber erst gemacht, nachdem ich die Tischplatte soweit zurechtgesägt hatte.
Was noch fehlte war der “Halteklotz” Dieser ist nachher für die Höhenverstellung zuständig. Der Halteklotz wird an die beiden Ständer geschraubt. Vorher bohrte ich genau in der Mitte des Klotzes ein 10mm Loch.
Der Ablagekasten
Der Ablagekasten dient nicht nur dazu herumfliegende Dinge verschwinden zu lassen, sondern ist ein wesentlicher Teil der Unterkonstruktion. Der Ablagekasten wird zwischen den beiden Ständerbeinen, also dem Teil der Beine, die mit dem Fuß verbunden sind, befestigt.
Übrigens ist auch der Ablagekasten aus der mir zugelaufenden MDF-Platte hergestellt. Wir wollen ja nicht nur Kosten, sondern auch Ressourcen sparen…
Die Teile werden also gemäß Sägeliste gesägt und mit Leim und Schrauben zusammengesetzt. Der Einbau erfolgt aber erst zum Schluß.
Die Hochzeit – Tischplatte und Unterkonstruktion
Die Beine müssen nun mit der Tischplatte verbunden werden.
Um eine stabile Verbindung herzustellen nahm ich jeweils drei Einschraubmuttern.
Um die seitlich an die Tischplatte auftretenden Kräfte abzufangen, habe ich zusätzlich jeweils drei 8 mm Holzdübel genommen, die ich nur in die Tischverbinder eingeleimt habe. So hatte ich später die Möglichkeit die Platte jederzeit abzunehmen, z.B. um sie nochmal zu lackieren.
Die Tischverbinder habe ich bereits mit drei Durchgangsbohrungen und drei Dübellöchern versehen.
Ich legte also die Tischplatte mit der Oberseite auf meinen Arbeitstisch und riss die Mitte von der Längsseite an.
Ich entschied mich nach längerem Nachdenken dafür die Tischverbinder nicht ganz mittig, sondern sie etwas nach vorne zu setzen. Das hatte folgenden Grund: Die Tischplatte ist etwas tiefer als die Füße lang sind. Da ich zusätzlich eine schwere Schublade im vorderen Teil der Füße sitzen habe, verschiebt sich der Schwerpunkt der Platte. Das habe ich mit dem Versetzen ausgeglichen.
Die Tischverbinder mit den Sperrholzbeinen wurden nun positioniert und die Löcher der Durchgangsbohrung entsprechend angezeichnet. Die Dübellöcher übertrug ich mit den Dübelspitzen.
Um die Einschraubmuttern einzubauen, bohrte ich gemäß Herstellerangaben vor und schraubte sie dann vorsichtig mit meinem größten Schlitzschraubendreher rein. Da MDF eine Faserplatte ist, merkte ich glücklicherweise recht schnell, dass die Vorbohrangabe hierfür etwas zu eng bemessen war. Beim Einschrauben entstand um die Mutter eine Erhebung, die zum Kippeln der Tischverbinder führte. Ich nahm also einen Bohrer, der um 0,5 mm größer war und alles war gut.
Die Schublade
Ich habe den Stellenwert einer abschließbaren Schublade für meine 6 jährige Tochter komplett unterschätzt.
Ja eigentlich stellte der Schreibtisch für meine Tochter erst wirklich einen konkreten Wert dar, nachdem ich ihr eröffnete eine abschließbare Schublade einzubauen (das hatte nämlich unser China-Mitbewerber-Produkt nicht…)
Wer vorher noch keine Schublade gebaut hat (so wie ich), dem sei an dieser Stelle empfohlen sich Zeit für den Bau zu nehmen. Vor allem wenn es um die richtige Anbringung der Auszüge geht.
Der Bau an sich ist nicht wirklich schwierig. Die Seitenteile hatte ich bereits vorgesägt und mit einer Nut für die Auszüge versehen. Die hintere Schubladenwand habe ich mit Schrauben und Leim mit den Seitenteilen verbunden.
Dann wollte ich die Front zurechtsägen und berechnen, wieviel länger sie sein muss, damit ich Platz für die Nut habe, die für den Boden erforderlich ist. Leider fiel mir erst jetzt auf, dass ich meine Oberfräse verliehen hatte…
Also Planänderung: der Boden stieß stumpf an die Front und wurde mit Leim und Drahtstiften, die ich von vorne durch die Front trieb, gesichert.
Da der Boden aus 10 mm Sperrholz besteht, sind die Seitenteile und die Rückwand konsequenterweise 10 mm niedriger als die Front. Der Boden wurde nach dem Zusammenbau der Schublade mit Holzdübeln und Leim auf die Unterseite aufgeleimt und mit Drahtstiften fixiert.
Der Einbau der Schublade war auch nicht so schwierig:
Den Tisch habe ich mit der Plattenoberseite auf meinen Arbeitstisch gelegt, die Beine und der Ablagekasten wurden ja schon montiert.
Die Schublade legt ich nun zwischen die Beine, so wie sie nachher sitzen sollte. Als Abstandshalter legt ich eine 2 mm Aluleiste unter die Schublade. (Kleiner Tip: nehmt min. 4 mm Abstand. Auch MDF arbeitet, bzw. biegt sich durch…)
Hinten am offenen der Nut zeichnete ich das Ende der Auszüge an. Jetzt zog ich die Schublade nach vorne und zog die Auszüge bis zur Markierung raus. Es erschien das erste Loch im Auszug in das ich jeweils die erste Schraube setzte. Da zog ich die Schublade weiter raus, schraubte wieder..zog raus…schraubte wieder…fertig!…
Mit den Nerven… jetzt erkannte ich, das der Auszug zu kurz war. Die Schubladenöffnung ragte gerade mal soweit unter der Tischplatte hervor, das ich unbequem einen Bleistift verstauen konnte…
Meine berüchtigten Seemannsgedichte kamen zum Einsatz und ich öffnete das erste Bier. Zum Glück! Den dabei fand ich zufällig zwei identsiche Auszüge, die knapp doppelt so lang waren! Das beweist: Bier trinken kann die Nerven beruhigen…
Also alles nochmal zurück und in der gleiche Reihenfolge wieder rein. Passt! Es folgte der unspektakuläre Einbau des Schlosses, das Setzen von zwei Stop-Blöcken für die Schublade und das genussvolle Austrinken des Bieres.
Die Höhenverstellung
Die Beine werden für die Höhenverstellung mit Löchern versehen, durch die nachher eine
Schloßschraube gesteckt und der Tisch dadurch arretiert wird. Die Schraube wird durch eine Mutter gesichert.
Das Gegenstück zum Halten ist der oben beschriebene “Halteklotz”.
Die Löcher habe ich im Abstand von jeweils 30 mm gebohrt. Leider habe ich hiervon kein Bild gemacht, aber auf der Skizze könnt Ihr die Maße entnehmen.
Fertig?
Unter normalen Umständen würde ich hier schreiben: “jetzt noch schnell lackiert und der Schreibtisch ist fertig” So war es aber nicht und warum, das beschreibe ich hier. Wen das nicht interessiert, der halte sich an den obigen Satz und clicke zu einem anderen Projekt…;-)
Das Lackieren
Da ich vorher noch kein MDF verarbeitet habe, geschweige denn lackiert habe, bin ich in den Baumarkt meines Vertrauens gefahren und habe mich bezüglich des Lacks beraten lassen.
Ich habe den ziemlich teuren Lack in der Wunschfarbe meiner Tochter anmischen lassen. Die Fachberaterin erklärte mir, weil MDF saugt, muss ich wahrscheinlich zweimal lackieren mit einem Zwischenschliff.
Ich muss gestehen, das ich kein Fan von Lackierarbeiten bin. Also so gar nicht, aber wat mutt dat mutt.
Ich fing also an die Platte und den Ablagekasten mit dem Lack zu lackieren. Er ließ sich gut rollen und ich war zufrieden. Mein Handy klingelt, ich drehe mich um, schaute wer mich anruft, weil ich wegen er Handschuhe nicht sofort rangehen konnte und drehte mich wieder zum Tisch.
DER LACK WAR WEG!!!! Weg.. wirklich nichts mehr zu sehen! Es gab zwar noch einige Schatten an der ich erkannte, dass ich nicht in einen Zeitstrudel gefallen bin, aber der Lack war sonst nicht mehr zu erkennen.
Ahhh… das meinte die Fachverkäuferin mit saugend. Gut darauf bin ich vorbereitet, ich habe genug Lack gekauft. Also machte ich mich daran mit einem anderen Lack (weiß, Kunstharzlack) die Beine inkl. Füße und Tischverbinder zu lackieren. Der blieb sichtbar.
Am nächsten Tag führte ich einen Zwischenschliff durch und lackierte munter drauf los. Ich will es hier abkürzen: Das einzige was sichtbar blieb war mein entgeistertes Gesicht… auch nach drei und vier Lackierungen (immer mit Zwischenschliff) gab es keine geschlossene farbige Fläche. Im Gegensatz zum Kunstharzlack… Weiterhin hat mit die Dame den falschen Farbton angemischt, aber den hat man ja sowieso nicht gesehen…
Ich beschloss meine Fachverkäuferin über diesen Tatbestand zu “informieren” und fuhr mit dem gekauften Lack zum Baumarkt.
Da sie an diesem Tag nicht arbeitete und mich drei andere Mitarbeiter abwimmeln wollten, musste ich meine Stimme leicht erheben (allerdings ohne Seemannsausdrücke) und verlangte mehr oder weniger höflich nach dem Abteilungsleiter.
Der stellte sich dann tatsächlich als Fachverkäufer heraus und erklärte mir leicht bestürzt, das ich MDF IMMER mit einer speziellen MDF-Vorstreichfarbe behandeln müsste und dann mit dem Lack weiterarbeiten könne.
Und jetzt verrate ich Euch einen Zauberspruch, der in so einer Situation immer zu einem besseren Ergebnis führt, als Ihr euch erhofft hattet (ich habe 16 Jahre Vertriebserfahrung…):
“Okay, was schlagen Sie vor?”
Auch hier die Abkürzung: Ich erhielt einen neuen Topf Lack mit dem richtigen Farbton, die MDF-Vorstreichfarbe und eine Packung Lackrollen – alles gratis!
Nun lackierte ich noch schnell den Schreibtisch und war fertig…:-)
Übrigens wurde ich ein paar Tage später als “Vater des Jahres” ausgezeichnet…
Einige Tage später war der Tisch bereits voll im Kinderzimmer integriert…