Hier nun die Beschreibung, wie ich meinen Tellerschleifer selbst gebaut habe.
Nachdem ich den Motor angeschlossen hatte und dieser zu meiner Zufriedenheit lief (Steinmetzschaltung), machte ich mich an den Rest.
Aus einem Ausverkauf hatte ich mir Schleifscheiben mit Klettverschluss mit einem Durchmesser von 405mm gekauft. Urspünglich wurden diese für Fußbodenschleifmaschinen verkauft.
Im Internet erwarb ich eine selbstklebende Haftscheibe in der passenden Größe.
Für die Scheibe leimte ich zwei 6mm Siebdruckplatten zusammen, die ich vorher mit meiner Bandsäge und der selbstgebauten Kreisschneidevorrichtung aussägte. Dabei entstand ein Loch genau in der Mitte, mit dem ich die Scheibe später ausbalancierte. Dazu legte ich eine Stahlkugel auf die Werkbank und legte die Scheibe mit dem Loch auf die Kugel. Die Scheibe kippte dabei immer zu einer Seite, was bedeutet, dass auf der gegenüberliegende Seite Material abgetragen werden musste. Das bewerkstelligte ich mit einem Forstnerbohrer, mit dem ich immer nur etwas Material entfernte. Dieser Prozess dauert ein wenig, ist aber für den späteren Rundlauf sehr wichtig.
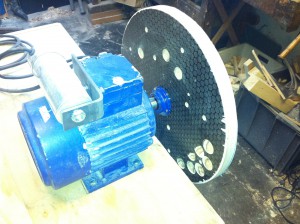
gut zu erkennen: die Löcher die ich zum Ausbalancieren der Scheibe bohrte
Nachdem die Scheibe also ausbalanciert ist, bohrte ich das mittlere Loch auf 8 mm auf. Ich hatte Glück, denn beim Motor war zum einen ein Flansch an der Welle montiert an der ich meine Tellerscheibe befestigen konnte und die Welle hatte an der Stirnseite ein M8-Innengewinde. Der Flansch hatte Zähne, die ich kürzte und für die ich Löcher in die Scheibe rund um das mittlere Loch bohrte. Ich schraubte also den Flansch auf den Teller, schob das Ganze auf die Welle und schraubte von vorne durch das Loch im Teller eine versenkbare M8 Schraube an die Welle, so dass sich nichts lösen kann. Auch das war Fummelkram, aber nachher passte alles wunderbar.
Jetzt kam der schwierigere Teil. Ich musste die Scheibe am Rand abdrehen.
Dazu befestigte ich den Motor auf meiner Werkbank und baute mir eine Auflage für das Abdrehwerkzeug – in meinem Fall ein Beitel von meiner Drechselbank.
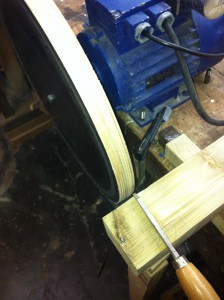
Ich ließ den Motor laufen und nahm vorsichtig von der Seite Material ab. SIe lief nicht so unrund wie ich befürchtete, weil ich die Scheibe ja mit der Kreisschneidevorrichtung schon recht rund aussägte.
Es entstand aber ein fürchterlicher Staub von der Siebdruckplatte, der meine ganze Werkstatt einhüllte. Zwei Beitel habe ich bei dieser Aktion durchgeglüht…
Als alles rund lief, klebte ich die Haftscheibe auf den Teller und setzte das Schleifpapier an.
Es funktionierte super!
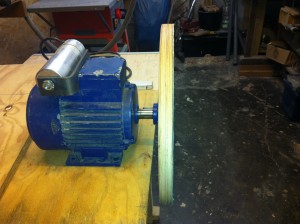
Es folgte nun der Tisch und der Rahmen.
Der Tellerschleifer sollte einen festen Platz in der Werkstatt bekommen. Also baute ich einen kleinen Tisch, der auf zwei Balken lagert und an der Wand angeschraubt ist.
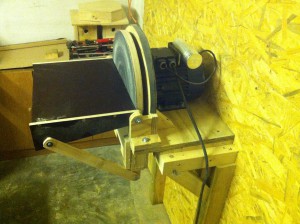
der eigentliche Tisch lagert auf zwei Balken, die an der Wand verschraubt sind
Um den Teller wollte ich ursprünglich einen Rahmen aus Alu setzen. Dazu sägte ich ein Brett 2 cm größer im Durchmesse als den Teller und sägte es in der Mitte durch. Ein Loch für die Welle kam noch rein und ich montierte diesen Schutz zwischen Motor und Teller.
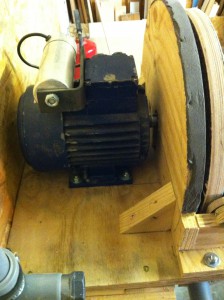
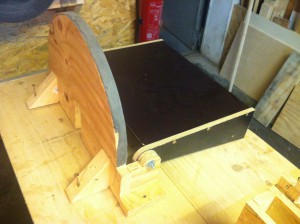
Der Rahmenhalter mit Auflage als Baugruppe
Ich stellte aber später für mich fest, dass ein Rahmen nur stört und nahm ihn wieder ab.
Mir war nicht ganz so wichtig unterschiedliche Winkel damit zu schleifen, deshalb entschied ich mich für eine einfache Auflage, die allerdings abgeklappt werden kann. Diese baute ich aus den Resten der Siebdruckplatte, weil die Oberfläche sehr glatt ist.
Die Auflage wird von zwei Bolzen rechts und links vom Tellerschleifer gehalten, an denen sie auch abgeklappt werden kann.
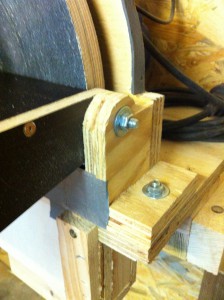
Die Auflage wird vorne von zwei Riegeln gehalten, die so ausgelegt sind, dass die Auflage exakt 90 Grad zum Tellerschleifer steht.
Damit war ich erstmal zufrieden, allerdings störte mich die teilweise erhebliche Staubentwicklung schon, so dass ich mich ziemlich kurzfristig entschloss, den Schleifer an meine zentrale Staubabsaugung anzuschließen.
Ein Rohr war schnell gelegt und ich musste den unteren Teil des Tellers staubdicht einhausen und ein flexibles Stück Schlauch dort anschließen.
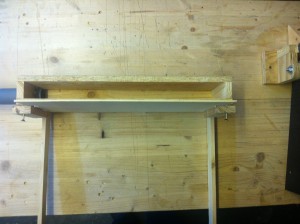
Der Staubfangkasten
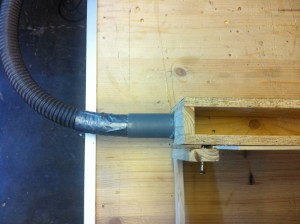
Ein flexibler Schlauch fest an den Kasten angeschlossen
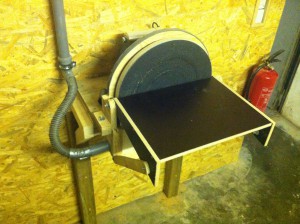
Der Tellerschleifer angeschlossen an die zentrale Staubabsaugung
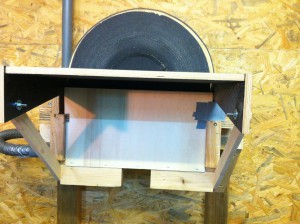
Den Spalt oben rechts am Kasten musste ich nachträglich abkleben
Ich benutze den Tellerschleifer sehr häufig und ich bin sehr froh, dass ich ihn gebaut habe. Das Schleifpapier in der Körnung 80 hält bereits seit einem halben Jahr und muss nun demnächst ausgetauscht werden. Auch die Absaugung funktioniert sehr gut.
Was jetzt noch fehlt, ist ein Schalter zum Ein- und Ausschalten, sowie ein Schalter für die Drehrichtung. Aber jetzt wird das Wetter ja allmählich schlechter…
