Für dieses Projekt nahm ich einfache Dachlatten und billige Leimholzplatten aus dem Baumarkt.
Die Dachlatten sägte ich mit der Kappsäge grob auf die Längen, die ich benötigte:
4 Stk. 900 mm (ich sägte 920 mm)
8 Stk. 320 mm (ich sägte 350 mm)
Wichtig ist hierbei darauf zu achten, dass sich in den abgesägten Stücken möglichst keine oder nur kleine Astlöcher und Beschädigungen befinden. Das verhindert aufwändige Spachtelarbeiten.
Im nächsten Schritt sägte ich mit meiner Tischkreissäge die Latten auf die Stärke 40×40 mm.
Mit dem Abrichthobel, hobelte ich zwei Seiten schön gerade und rechtwinkling zueinander. Danach ging es durch den Dickenhobel, den ich auf 35 mm eingestellt habe.
Ich war ganz froh darüber, dass ich die Leisten etwas länger gelassen habe, weil der Dickenhobel beim ersten und letzten Stück jeweils am Anfang und dann am Ende eine Vertiefung hinterlässt. Das kann man normalerweise dadurch verhindern, indem man ein Opferstück zuerst und ganz zum Schluss einschiebt und dann die Leisten stramm hintereinander durchziehen lässt. Das habe ich natürlich nicht gemacht… beim nächsten mal vielleicht…
Einmal habe ich nicht aufgepasst und da hat der Dickenhobel die Leiste ganz blöde erwischt, so dass dort viel zuviel Material abgenommen wurde…
Besonders gespannt war ich auf mein neues Undercover-Jig von Wolfcraft. Ich habe schon viel gelesen und auf youtube gesehen über “pocket holes” und “verdeckte Holzverschraubungen”. Nun will ich das mal selbst ausprobieren.
Den Rahmen der Lampe montierte ich in zwei Schritten. Als erstes habe ich zwei Holzrahmen gebaut, die dann zu einem Kasten zusammengesetzt wurden.
Die Rahmen wurden von oben mithilfe des Stufenbohrers mit pocket holes versehen, verleimt und verschraubt. Die Handhabung des Jigs ist denkbar einfach. Die Schablone wird anhand der Holzstärke eingestellt, der Stufenbohrer mit einem Tiefenstop in der Tiefe begrenzt. Schon kann es losgehen.
Marc von www.ich-bin-heimwerker.de hat ein Video von der Handhabung gemacht. Hier gehts zum Video
Ich hätte nicht gedacht, dass diese Verbindung so gut hält!
Es folgte der zweite Rahmen. Durch diese für mich neue Verbindungsmöglichkeit geht das Ganze recht schnell.
Nachdem beide Rahmen fertig waren, habe ich sie mit 120er Schleifpapier und meinem Excenterschleifer schön geschliffen.
Im nächsten Step verband ich die beiden Rahmen zu einem Kasten. Die Vorgehensweise ist die Gleiche wie bei den Rahmen.
Wichtig ist dabei immer der Einsatz von Schraubzwingen, weil sich die Werkstücke sonst beim Verschrauben verziehen können.
Die Löcher werden nachher durch die Boden- und Deckplatte verdeckt.
Wo wir auch schon beim nächsten Schritt angelangt sind: Der Boden- und Deckplatte.
Hierfür kaufte ich 18 mm starke Leimholzplatten aus dem Baumarkt. Sie sind sehr günstig und nicht besonders hochwertig (Astlöcher, etc.), aber da sie später lackiert werden sollen, ist das nicht so schlimm.
Sowohl die Boden- als auch die Deckplatte bestehen aus zwei verleimten Platten, die einen Versatz von 30 mm haben.
Das Leimholz ist 400 mm breit und nachdem ich die erste Platte auf 400 x 400 mm gesägt und den Kasten drauf gestellt hatte, sah es etwas “unterrepräsentiert” aus… Das bedeutet, dass die untere Platte 30 mm auf jeder Seite breiter sein muss, damit die Optik stimmt. Das war mit den 400er Leimplatten aber nicht möglich und breitere gab es nicht.
Ich hatte noch gehobelte Bretterabschnitte aus einem anderen Projekt liegen, die etwa 20 mm stark waren. Aus diesen baute ich einen Rahmen und leimte und schraubte die 400er Bodenplatte darauf. Da es sich ja um die Bodenplatte handelt, sieht man nicht, dass es sich nur um einen Rahmen handelt.
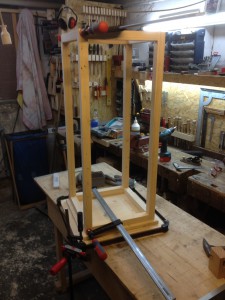
der Rahmen wird gehalten von einem Rahmenspanner bis der Leim trocken ist
Für die Deckplatte wollte ich aber zwei ganze Platten nehmen.
Dazu sägte ich von einem anderen Leimholzbrett 7 cm längs ab und leimte es an ein weiteres Leimholzbrett. So kam ich auf 470 mm.
Ja, ich weiß, das hätte ich auch bei der Bodenplatte machen können…da hatte ich aber diese Idee noch nicht.
Die fertige Leimplatte habe ich jetzt auf das richtige Maß (460×460 mm) gesägt und mit der kleineren Platte (400×400 mm) verleimt und verschraubt.
Es folgt das Loch für die Deckplatte. Das habe ich ganz unspektakulär mit einer Lochsäge ausgeschnitten, nachdem ich die Mitte angezeichnet habe.
Das Loch soll von einer Aluplatte verdeckt werden, die auf vier Aluröhrchen sitzt. Also habe ich auch gleich die vier 6mm Löcher für diese Röhrchen gebohrt.
Die Aluplatte ist 2 mm stark und ich habe sie auf die Maße 200×200 mm gesägt. Das ging mit der Bandsäge und einem Holzsägeblatt sehr gut.
Um die Röhrchen mit der Aluplatte zu verbinden habe ich vier 4 mm Löcher in die Platte gebohrt. Das Innenmaß der Röhrchen beträgt auch 4 mm. Das ist sehr gut, weil die Poppnieten, die ich noch vorrätig hatte zufällig auch 4 mm Durchmesser haben. Also habe ich die Röhrchen mit den Poppnieten an der Platte befestigt.
Es folgte der Bau der Tür. Auch diese besteht aus einem einfachen Rahmen, den ich aber in diesem Fall mit PU-Kleber geklebt habe.
Ich wollte keine Scharniere für die Tür nehmen, deshalb habe ich zwei Stücke von den Röhrchen abgesägt, ein 6 mm Loch oben und unten an der Ecke in den Rahmen gebohrt, in denen die Röhrchen gesteckt werden.
In den Kasten habe ich ebenfalls zwei 6 mm Löcher gebohrt, als Aufnahme für die Röhrchen der Tür. Dabei habe ich bei der Oberseite eine Durchgangsbohrung gemacht, die Tür unten mit drei Unterlegscheiben eingesetzt und die Röhrchen von oben durch den Rahmen in die Tür geschoben.
Wie sollte jetzt aber die Tür halten? Durch einen Riegel? Nö! Hier kommen wieder meine Power-Magneten ins Spiel, ich ich auch bei meinem Buchständer eingesetzt habe!
Einen Magneten habe ich in die Tür eingelassen und einen auf gleicher Höhe in den Rahmen. Eingeklebt habe ich sie mit Epoxy-Kleber.
Zusätzlich zu den Magneten habe ich aber noch einen Anschlag angebracht, damit die Tür nicht schwungvoll nach innen schlagen kann und eventuell die Deko ruiniert…
Die nächste Frage betraf den Henkel. Ja, richtig… Henkel!
Meine Frau wollte einen Henkel, um das Monstrum von Windlicht rein- und raustragen zu können…
Dazu befestigte ich zwei Holzblöcke rechts und links auf dem Deckel, nachdem ich jeweils ein 8 mm Loch in die Blöcke gebohrt habe. Ich habe sie schlicht mit PU-Kleber geklebt.
Den Henkel baute ich aus Holzresten. Den Griff habe ich mit dem Hobel und meinem Tellerschleifer geformt.
Während ich so mit meinem Tellerschleifer die Rundungen schliff, roch es etwas verbrannt. Der Geruch wurde immer intensiver und ich schaltete alles ab, was in meiner Werkstatt lief.
Tja, was soll ich sagen… mein seit Jahren treuer Begleiter, der Nilfisk Staubsauger ist nun nach noch nicht mal ganz zwanzig Jahren kaputtgegangen… Er ist quasi in Rauch aufgegangen…
Aber von solchen kleinen Rückschläge lassen wir uns Heimwerker ja nicht aus dem Takt bringen. Ich hatte noch einen alten Haushaltsstaubsauger, den ich kurzerhand an meinen Zyklonen anschloss und weiter baute…
Den Griff habe ich mit PU-Kleber verleimt.
Der nächste Arbeitsschritt bestand darin, die Boden-und die Deckplatte an den Kasten anzuschrauben und zusätzlich zu verleimen. Das war eher unspektakulär und wurde deshalb auch nicht mit einem Bild gewürdigt… naja… ich hab vergessen es zu fotografieren…
Ja es sah wirklich schon gut aus, aber etwas fehlte und ich kam nicht drauf, was es sein könnte.
Morgens beim Duschen kam mir der richtige Gedanke… die Füße fehlen!
Also nach Feierabend wieder in den Keller und die Füße zurechtgesägt, mit dem Halbrundfräser eine Seite abgerundet, geschliffen und angeklebt… Ihr ahnt es… mit PU-Kleber
Das Plexiglas haben wir nun besorgt, jetzt ging es ans zuschneiden.
Es handelt sich eigentlich um sogenanntes Bastelglas, ist 2 mm stark und recht flexibel und eher weich. Ich habe es mit dem Cuttermesser und einem Stahlwinkel geschnitten. Das ging sehr gut, war sauber und man hat quasi keinen Verschnitt. Sägen mit der Bandsäge oder Tischkreissäge ist schwierig, weil durch die Hitzeentwicklung das Material zum Schmelzen neigt.
Um die Scheiben einzufassen habe ich 10 mm Holzleisten an der Tischkreissäge geschnitten. Damit werden die Scheiben von vorne und hinten eingefasst, also brauchte ich 16 lange und 16 kurze Leisten.
Um diese dünnen Leisten sicher an der Tischkreissäge schneiden zu können, habe ich mir ein dünnes Brett rausgesucht, vorne einen langen Absatz eingesägt und hinten 10 mm stehengelassen. Damit konnte ich die Leisten sicher an dem Sägeblatt vorbeiführen.
Nun waren die Teile sägerauh. Heißt: Schleifen. Das ist aber sehr müßig, weil diese dünnen Dinger hin und her wackeln und das alles sehr unhandlich ist.
Aus einer Laune heraus schnappte ich mir meinen Hobel und versuchte es damit.
Klappte super und ging viel schneller!
Jetzt kommt der Teil, den ich bisher immer versucht habe zu vermeiden… das Lackieren. Ich gebe es zu: ich hasse es zu lackieren, zu malen, zu tapezieren. Ich reiße lieber eine Wand ein, als Fußleisten zu lackieren sehr zum Leidwesen meiner Frau…
Weil diese Lampe so viele Ecken und Winkel hat, wollte ich nicht mit dem Pinsel oder der Rolle lackieren, sondern die Sprühpistole von ALDI nutzen, die ich mir von meinem Vater..äh… organisiert… also langzeit-ausgeliehen habe.
Ich mach es kurz: es ging nicht, die Pistole lief, aber es kam kein Lack raus. Es war 19.46 Uhr und ich wollte unbedingt mit einer Feinsprühpistole diese olle Laterne lackieren!
Also ab ins Auto, zum Baumarkt und die Wagner 550 Feinsprühpistole eingepackt, nach Hause gefahren, ausgepackt, Lack eingefüllt und lackiert.
Jetzt finde ich Lackieren doch nicht mehr so doof. Es ist echt einfach und bringt gute Ergebnisse. (Nein, das ist kein gesponserter Artikel…!) Demnächst berichte ich detaillierter über dieses Werkzeug.
So, die erste Lackschicht (Lack mit etwa 15% Wasser verdünnt) ist aufgetragen. Dann fiel mir ein, dass es doch ganz nice wäre, wenn ich die äußeren Scheibenleisten (nenn ich mal so) gleich im zweiten Durchgang mit “einlackieren” würde.
Die Leisten habe ich einmal vorlackiert und dann kurz übergeschliffen um die Fasern, die sich teilweise aufgestellt haben, zu entfernen.
Die Leisten habe ich auf Länge gesägt, eingepasst, mit wasserfesten Holzleim verleimt und mit Pins getackert.
Nachdem alle Leisten einsetzt wurden, fiel mir auf, dass ich nur 8 lange Leisten geschnitten habe… Vielleicht wurden sie auch geklaut…? Wie auch immer, ich musste also nochmal 8 Stück schneiden und lackieren. Da der zweite Lackiervorgang anstand ging es also in dieser Reihenfolge weiter.
Es folgte der letzte Lackiervorgang. Ich will hier nicht näher auf das Lackieren eingehen, da ich absolut kein Fachmann auf diesem Gebiet bin. Es war auf jeden Fall alles voller Lack…alles! Aber egal, darum kümmere ich mich später.
Als der Lack trocken war, setze ich die Scheiben mit den Scheibenleisten ein. Die Scheibenleisten habe ich nicht geleimt, um ein eventuell erforderliches Auswechseln möglichst einfach zu machen. Sie wurden also nur mit Pins getackert.
Mit einem kleinen Pinsel besserte ich noch einige kleinere Stellen aus, vor allem an den inneren Scheibenleisten.
Die Tür habe ich mit einem einfachen Möbelknopf aus Edelstahl versehen.
Den Aludeckel befestigte ich, in dem ich die Röhrchen mit Epoxykleber in die vorhandenen Löcher steckte.
Als letzen Arbeitsschritt montierte ich den Griff und bestaunte mit großen Kinderaugen die Laterne… und die Uhr….
Ich glaube ich habe mich bei noch keinem Projekt so mit der Zeit verschätzt, wie bei diesem…
Aber die Laterne ist wirklich schön geworden.
Was würde ich anders machen?
Ich würde keine Scheibenleisten mehr verwenden, sondern gleich zu Beginn eine Nut ein die Rahmen sägen, in die die Scheibe nachher eingeschoben werden kann. Dazu muss der Deckel zuletzt befestigt werden.
Ich glaube auch, beim nächsten Mal würde ich doch Glas verwenden. Das Plexiglas ist sehr statisch, zieht somit Staub an und sieht immer etwas schmutzig aus.
Das ganze Projekt hat mich etwa 55 € gekostet, wovon die Plexiglasscheiben schon 44 € gekostet haben.
Meine Frau meint, dass sei nicht die letzte Laterne gewesen, die ich gebaut habe…
Pingback: Monster-Laterne bei Kellerwerker
Pingback: Blogrundschau Holz Technik 45/2014 - Heimwerker-Blog
Pingback: ProKilo Metall- und KunststoffmarktFünf Dinge, die du in der kalten Adventszeit dringend brauchst!
Ich habe jetzt zu Halloween dank deiner Anleitung zwei tolle Laternen gebaut. Vielen Dank für deine Anleitung!