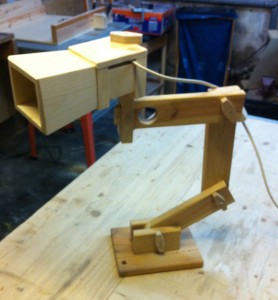
Die Holzlampe… ein Traum in Holz…
Alle Teile der Lampe bestehen aus Restholz. Nur die Schrauben und die Gewindestangen sind neu. Die Lampenfassung mit Kabel und Kabelschalter habe ich aus einer alten IKEA-Lampe ausgebaut. Soweit ich es bis hierher beurteilen kann, hat meine Frau das noch nicht bemerkt…
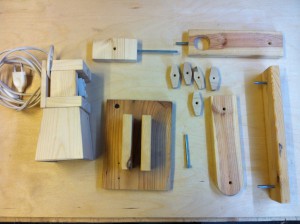
Bauteile der Holzlampe
Die Holzmuttern
Im ersten Schritt habe ich die benötigten Holzmuttern hergestellt. Eigentlich war ich nur zu bequem, um in den Baumarkt zu fahren und mir Flügelmuttern zu besorgen. Mittlerweile bin ich ein großer Fan von diesen Holzmuttern, weil ich sie einfach schicker finde.
Für die Holzmuttern suchte ich mir die Sägereste einer 30mm Birken-Multiplexplatte zusammen und sägte sie mit der Bandsäge in eine Salmi-Form mit stumpfen Enden. Mit dem Tellerschleifer bearbeitete ich die Ränder, bis alles ordentlich aussah. Danach teilte ich die Stücke in der Mitte, so dass ich zwei Salmis mit 15mm Stärke erhielt. Wo ich schon mal dabei war, sägte ich gleich 20 Stück aus und legte sie mir für spätere Projekte aufs Lager.
Für das Gewinde bohrte ich mit einem 3,5 mm Bohrer in der Mitte ein Loch und schnitt dann mit einem M5-Gewindeschneider das Gewinde ein. Fantastisch wie belastbar diese Mutter tatsächlich ist!
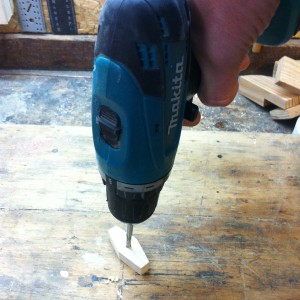
Gewindeschneiden
Der Fuß
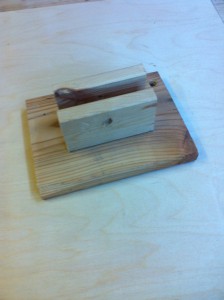
Lampenfuß
Der Fuß besteht aus einem Brett (18x14cm), auf dem zwei Holzklötze (10×5,5cm) montiert sind zwischen denen der erste Schenkel befestigt wird. Die Klötze wurden im Abstand der Stärke der Schenkel 5,5cm) verleimt und von unten verschraubt. Im Anschluß habe ich mittig eine 5mm Durchgangsbohrung gesetzt. Hier wird die Schraube durchgesteckt, die das nächste Teil hält:
Der abgerundete Schenkel
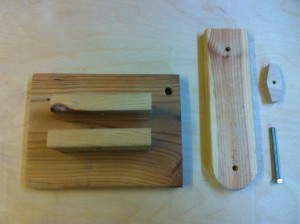
Holzfuß mit ersten Schenkel
Es folgt der erste Schenkel, der unten zum Fuß hin abgerundet sein muss. Der Schenkel ist 20cm lang und 5,5cm breit. Zwei 5mm Bohrungen wurden mittig – 25mm von den Enden gesetzt. Mit einer M5 Maschinenschraube montierte ich den Schenkel am Fuß und fixierte ihn mit der Holzmutter.
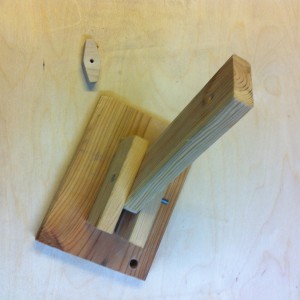
Holzfuß mit Schenkel montiert
Es folgt der nächste Schenkel:
Der Mittelschenkel
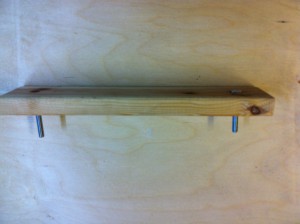
Der Mittelschenkel
Der Mittelschenkel ist 26cm lang und auch 5,5cm breit. Hier sind nur zwei 5mm Bohrungen erforderlich, die jeweils 25mm von den Stirnseiten mittig gesetzt werden. Auch hier kommen M5 Maschinenschrauben zum Einsatz, die ich mit gezielten Hammerschlägen soweit ins Holz trieb, dass der Schraubenkopf im Holz versenkt ist. Bei Hartholz würde ich entsprechend vorbohren – in meinem Fall habe ich Fichte genommen, dadaurch ging es auch ohne.
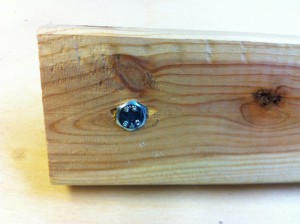
Man kann die aufgewendete Kraft nur erahnen, die erforderlich war, um dieses massive Stück Metall ins Holz zu treiben…
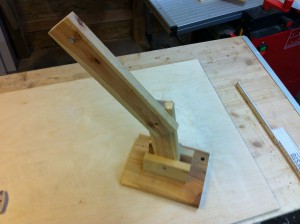
Der montierte Mittelschenkel
Der Mittelschenkel wird mit einer Holzmutter am ersten Schenkel montiert. Es folgt
Der Oberschenkel
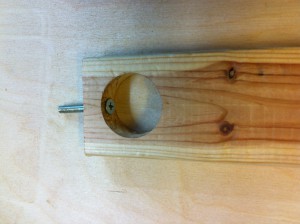
Da ich ursprünglich dieses Gestell als Halter für meinen Staubsaugerschlauch nutzen wollte, habe ich im vorderen Bereich 10mm von der Stirnseite ein 35mm großes Loch gebohrt. Im Nachhinein war das eine gute Idee, denn dadurch konnte ich den Lampenkorb drehbar gestalten.
Übrigens sind die 10mm in diesem Fall zu wenig, weil bei zuviel Druck die Schraube das Material spaltet… Mehr dazu ganz am Ende beim Thema “Was würde ich bei der nächsten Lampe anders machen…”
Der Oberschenkel misst 20cm Länge und 5,5cm Breite. Eine 5mm Bohrung kommt wieder an die eine Stirnseite (also wieder 25mm davon entfernt) und eine 5mm Bohrung kommt mittig durch das Hirnholz auf der Seite mit der 35mm Bohrung.
Flugs den Oberschenkel an den mittleren Schenkel mittels Holzmutter montiert und weiter gehts.
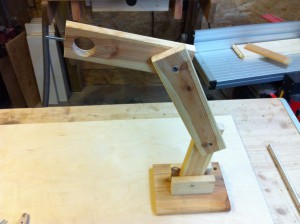
montierter Oberschenkel
Kommen wir nun zur
Lampe
Die Lampenfassung hat zwar ein Außengewinde, allerdings war das nur 20mm lang und eine Kontermutter hatte ich dafür auch nicht. Ich nahm also ein Reststück einer 20mm Fichtenplatte, sägte zwei Stücke á 80x65mm zurecht und bohrte in eines davon ein 30mm Loch. Als Deckel nahm ich eine 10mm starkes Brettchen, das auf die Maße 80x90mm gesägt wurde. Rechts und linke leimte ich jeweils ein Klötzchen mit 45x50mm und 20mm Stärke ein. Zum Deckel und nach unten habe ich 10mm Platz gelassen. Das Kabel führte ich durch den oberen Spalt.
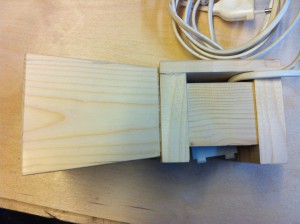
Die Lampe mit Lampenkorb
Nun folgte der
Lampenkorb
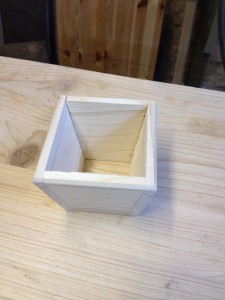
Der Lampenkorb
Ich sägte aus einem 10mm Fichtenbrett zwei Teile á 95x95mm und zwei Teile á 95x85mm aus. Die beiden Teile, die jeweils oben und dunten sitzen wurden zu der einen Seite hin auf 75mm , die anderen beiden Teile auf 65mm gekürzt. Damit ergibt sich ein sich nach außen öffnender Lampenkorb. Warum nicht alle Seiten auf 75mm gesägt wurden? Ganz einfach… ich habe mich bei dem einen Teil versägt und hatte keine 10mm Plattenabschnitte mehr… Ich hätte auch schreiben können:” Um die Lichtverteilung eher seitlich zu begünstigen habe ich den Lampenkorb etwas abgeflacht konstruiert…”, aber Euch kann ich ja die Wahrheit sagen…
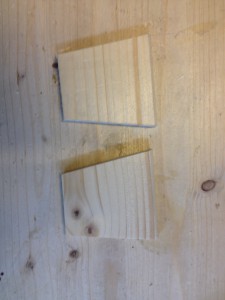
Wie fixiert man nun so eine Konstruktion um sie ordentlich verleimen zu können? Mit Keilen!
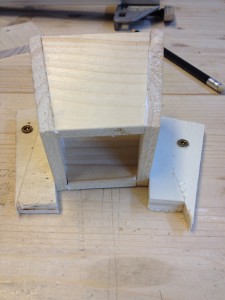
Kleine Keilerei
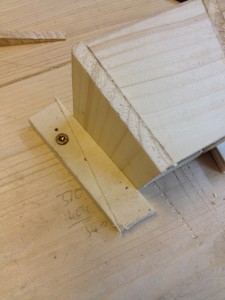
Ich schnitt mir aus 10mm Sperrholzresten kleine Keile zurecht, bohrte in zwei Keile ein Loch für eine Spaxschraube, legte mir die zu verleimenden Teile mit den Keilen zurecht und schraubte sie an der Arbeitsplatte meines Arbeitstisches fest – aber so, dass sie sich noch drehen ließen. Nachdem die unteren Kanten mit Leim versehen wurden, setze ich alle Einzelteile zusammen – wobei die obere Platte trocken eingesetzt wurde und drückte vorsichtig die losen Keile zwischen die festen Keile und das Werkstück. Simsalabim…! Hat super geklappt! Als der Leim abgebunden hat, wiederholt ich das Spiel mit der anderen Seite.
Als alles fest war, schliff ich den Korb mit 120er Schleifpapier und brach die Kanten.
Den Korb leimte ich danach auf die Lampe.
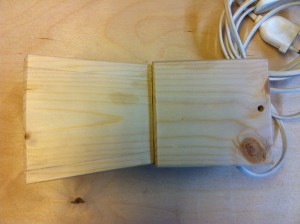
Lampe und Lampenkorb glücklich vereint…
Um die Lampe schließlich in alle Richtungen bewegen zu können, fehlt noch ein Bauteil für das ich lange keinen Namen fand. Darum heißt es jetzt einfach
Lampenaufnahme
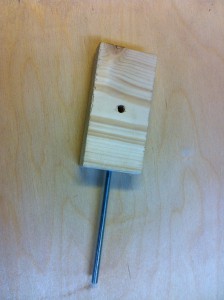
Lampenaufnahme
Die Lampenaufnahme ist eigentlich nur ein kleines Stück 20mm starkes, 5cm breites und 8cm langes Stück Holz mit einem 5mm Loch in der Mitte und einer 10cm langen M5-Gewindestange. Die Gewindestange sitzt in einem ins Holzstück vorgeschnittenem M5-Gewinde.
Die Lampenaufnahme wird nun an den Oberschenkel geschraubt, wobei die Gewindestange nach obern gerichtet ist.
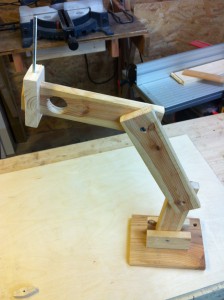
Lampenaufnahme am Oberschenkel montiert
In die hintere Platte der Lampe, wird eine 5mm Durchgangsbohrung gesetzt, sodass die Lampe auf die Lampenaufnahme aufgesteckt werden und mit der letzten Holzmutter befestigt werden kann.
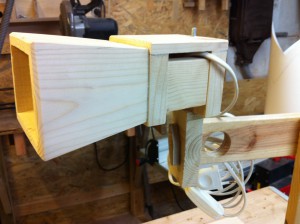
Lampe auf Lampenaufnahme gesteckt
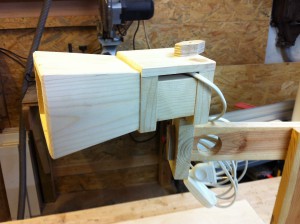
und mit Holzmutter befestigt
Ich habe nachträglich noch ein 8mm Loch in eine Ecke des Holzfußes gebohrt, um die Lampe an meinen Tisch, auf dem die Bohrmaschine steht anschrauben zu können.
Fertig ist die Holzlampe!
Da die Lampe ausschließlich in der Werkstatt genutzt wird, habe ich sie weder lackiert noch geölt.
Was würde ich bei der nächsten Lampe anders machen?
Sollte ich mal wider Erwarten eine Lampe für mein Büro bauen, würde ich einige konstruktive Änderungen vornehmen. Zum Beispiel würde ich am Oberschenkel kein 35mm Loch bohren, sondern die Lampe direkt und ohne zusätzliche Lampenaufnahme daran befestigen. Wahrscheinlich würde ich auch die Kabelführung, sowie den Lampenkasten etwas anders gestalten. Nicht als halboffenen Kasten, sondern als geschlossenen Kasten. Die Wärmeentwicklung ist durch den Einsatz einer Energiesparlampe sehr gering.
Natürlich würde ich auch die Oberfläche ordentlicher bearbeiten und das Ganze ölen.